Plastic extrusion specialists delivering exactness and quality
A Comprehensive Overview to the Process and Advantages of Plastic Extrusion
In the substantial world of manufacturing, plastic extrusion emerges as a crucial and extremely effective process. Translating raw plastic into constant profiles, it provides to a plethora of markets with its amazing adaptability.
Recognizing the Essentials of Plastic Extrusion
While it may appear complicated initially glimpse, the procedure of plastic extrusion is basically simple - plastic extrusion. It is a high-volume manufacturing strategy in which raw plastic is melted and shaped into a constant profile. The procedure starts with the feeding of plastic product, in the type of granules, pellets, or powders, into a heated barrel. The plastic is then melted utilizing a mix of warm and shear, applied by a revolving screw. As soon as the molten plastic gets to completion of the barrel, it is forced with a small opening called a die, forming it into a wanted kind. The designed plastic is after that cooled, solidified, and cut into desired lengths, finishing the procedure.
The Technical Process of Plastic Extrusion Explained

Kinds of Plastic Suitable for Extrusion
The option of the appropriate sort of plastic is a crucial aspect of the extrusion procedure. Various plastics supply unique buildings, making them extra suited to specific applications. Polyethylene, as an example, is frequently utilized as a result of its inexpensive and simple formability. It offers superb resistance to chemicals and moisture, making it suitable for items like tubes and containers. Similarly, polypropylene is another preferred option as a result of its high melting factor and resistance to fatigue. For more robust applications, polystyrene and PVC (polyvinyl chloride) are typically chosen for their strength and longevity. These are common alternatives, the choice ultimately depends on the specific needs of the product being created. So, comprehending these plastic types can substantially boost the extrusion procedure.
Contrasting Plastic Extrusion to Other Plastic Forming Approaches
Comprehending the types of plastic appropriate for extrusion leads the way for a broader discussion on exactly how plastic extrusion piles up against various other plastic forming approaches. These include shot molding, impact molding, and thermoforming. Each approach has its distinct usages and benefits. Shot molding, for instance, is exceptional for developing intricate components, while impact molding is excellent for hollow items like bottles. Thermoforming excels at forming superficial or huge components. Nonetheless, plastic extrusion is unequaled when it involves creating continual accounts, such as pipes, gaskets, and seals. It additionally permits for a constant cross-section along the length of the item. Hence, the selection of approach mainly depends on the end-product demands and specs.
Secret Advantages of Plastic Extrusion in Manufacturing
In the world of manufacturing, plastic extrusion offers numerous considerable benefits. One notable advantage is the cost-effectiveness of the process, which informative post makes it an economically appealing manufacturing approach. In addition, this strategy gives superior item flexibility and enhanced manufacturing rate, therefore increasing overall production efficiency.
Cost-efficient Production Approach
Plastic extrusion jumps to the center as an economical production technique in manufacturing. Furthermore, plastic extrusion calls for much less power than traditional click here for info manufacturing techniques, adding to reduced functional prices. In general, the monetary advantages make plastic extrusion a very eye-catching choice in the production market.
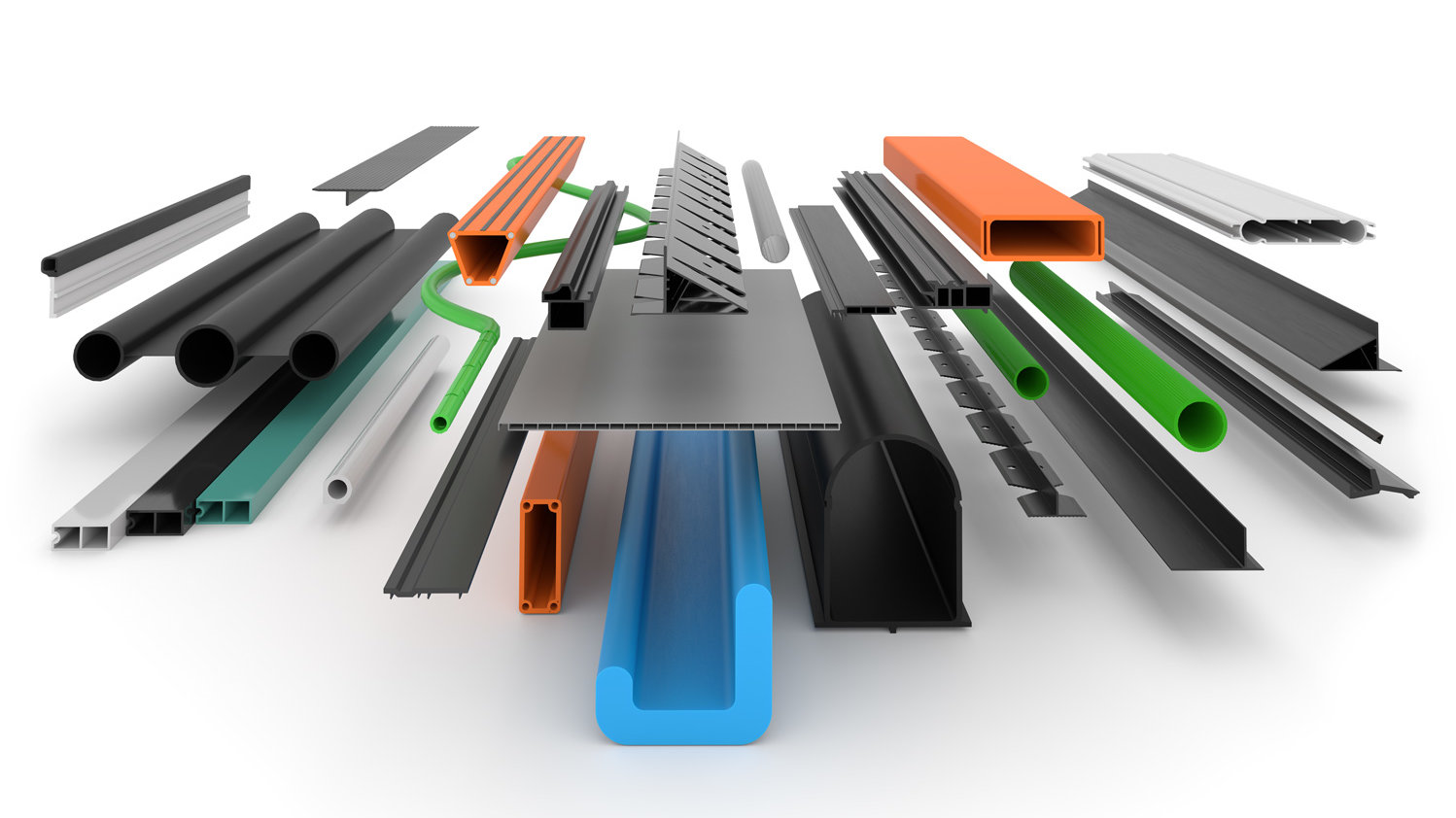
Superior Item Flexibility
Past the cost-effectiveness of plastic extrusion, another substantial benefit in making hinge on its remarkable product flexibility. This process permits for the development of a wide array of products with varying designs, forms, and sizes, from easy plastic sheets to elaborate accounts. The versatility is credited to the extrusion die, which can be customized to yield the preferred product layout. This makes plastic extrusion a perfect solution for sectors that need personalized plastic parts, such as automotive, building, and packaging. The capability to create diverse products is not just useful in conference specific market demands yet likewise in allowing producers to check out new item lines with very little funding investment. Basically, plastic extrusion's product versatility fosters advancement while enhancing functional performance.
Improved Manufacturing Speed
A considerable advantage of plastic extrusion lies in its improved manufacturing rate. This manufacturing process enables for high-volume manufacturing in a relatively short time period. It is qualified of generating long, continuous plastic profiles, which significantly lowers the production time. This high-speed manufacturing is especially helpful in sectors where large amounts of plastic parts are needed within limited target dates. Few other manufacturing processes can match the speed of plastic extrusion. Additionally, the capacity to preserve constant high-speed production without compromising product high quality establishes plastic extrusion in addition to various other approaches. The improved production speed, as a result, not only allows producers to meet high-demand orders but also adds to raised performance and cost-effectiveness. This helpful function of plastic extrusion has made it a recommended selection in countless sectors.
Real-world Applications and Effects of Plastic Extrusion
In the realm of manufacturing, the method of plastic extrusion holds profound significance. This procedure is extensively utilized in the production of a selection of products, such as plastic tubing, home window frameworks, and weather removing. Because of this, it greatly affects markets like building, packaging, and automotive sectors. Moreover, its influence includes day-to-day products, from plastic bags to tooth brushes and non reusable flatware. The financial advantage of plastic extrusion, primarily its cost-effective and high-volume outcome, has actually reinvented manufacturing. Nonetheless, the ecological impact of plastic waste remains a problem. The market is persistently striving for technologies in recyclable and biodegradable materials, suggesting a future where the advantages of plastic extrusion can be retained without endangering ecological sustainability.
Conclusion
Finally, plastic extrusion is a efficient and extremely discover this effective technique of transforming resources into diverse products. It supplies numerous benefits over various other plastic creating approaches, consisting of cost-effectiveness, high output, minimal waste, and design versatility. Its effect is exceptionally felt in numerous sectors such as construction, automobile, and durable goods, making it an essential procedure in today's manufacturing landscape.
Delving much deeper right into the technical process of plastic extrusion, it starts with the option of the ideal plastic material. When cooled, the plastic is cut right into the called for sizes or wound onto reels if the product is a plastic movie or sheet - plastic extrusion. Contrasting Plastic Extrusion to Other Plastic Forming Methods
Comprehending the types of plastic ideal for extrusion paves the way for a more comprehensive conversation on how plastic extrusion stacks up versus various other plastic developing techniques. Few various other production processes can match the speed of plastic extrusion.